Hardening and Tempering
Case Hardening
Carburizing & Annealing
Solutionizing & Aging
Normalizing
Annealing
Stress Relieving
Stabilizing
Hardening and Tempering

Treatment Processes: Hardening and tempering typically involve heating steels to their hardening temperature (around 800-900°C), followed by rapid cooling (quenching) and tempering at a lower temperature. Specialized options like martempering and austempering provide alternatives based on alloy content and component size. “Neutral hardening” in a protective environment is used for applications requiring scale-free and decarburization-free surfaces.
Benefits: Hardening and tempering yield an optimal balance of hardness, strength, and toughness, allowing for weight and material savings. This process enables the machining or forming of components in a soft state before achieving high mechanical properties through heat treatment. Components like nuts, bolts, springs, and bearings benefit from precision achieved through neutral clean hardening.
Steels Suitable for Treatment: Nearly all engineering steels containing over 0.3% carbon respond to hardening and tempering. Standards like BS970 and BS EN 10083-1 and -2 provide a comprehensive list of hardenable steels. Specialized standards cater to specific applications, such as aircraft standards (e.g., “S” standards), fasteners (BS3111), and springs (BS5770).
Limitations and Considerations:- Hardening Response: Varied responses based on steel composition, size, and treatment method.
- Negative Effect of Aluminum: Aluminum in certain steels can affect hardening response; careful monitoring and steel supplier certification are essential.
- Steel Condition: Surface layers must be inspected and machined if purchased after open treatments. Cold-worked conditions may contain residual stresses requiring removal before hardening.
- Temper Embrittlement: Some steels may suffer embrittlement if tempered within a specific temperature range (250-450°C).
- Component Size and Shape: Considerations for distortion or cracking based on the size, shape, and the heat treater’s equipment capacity.
- Distortion or Cracking: Arises from various causes; careful component design, material selection, and early consideration of potential issues are crucial.
- Scaling and Decarburization: Open furnace treatment may lead to scaling and decarburization; alternative options like clean/neutral hardening exist to prevent these issues.
- Mixed Batches: Components from mixed material batches can respond differently to hardening treatment, leading to rejections and additional costs.
- Use quality steel from reputable suppliers.
- Design components with heat treatment in mind.
- Consult with heat treaters early in the design phase.
- Specify the right steel for the required hardness and section size.
- Remove surface defects before treatment.
- Consider stress relieving to minimize distortion.
- Account for post-heat-treatment processes.
Case Hardening
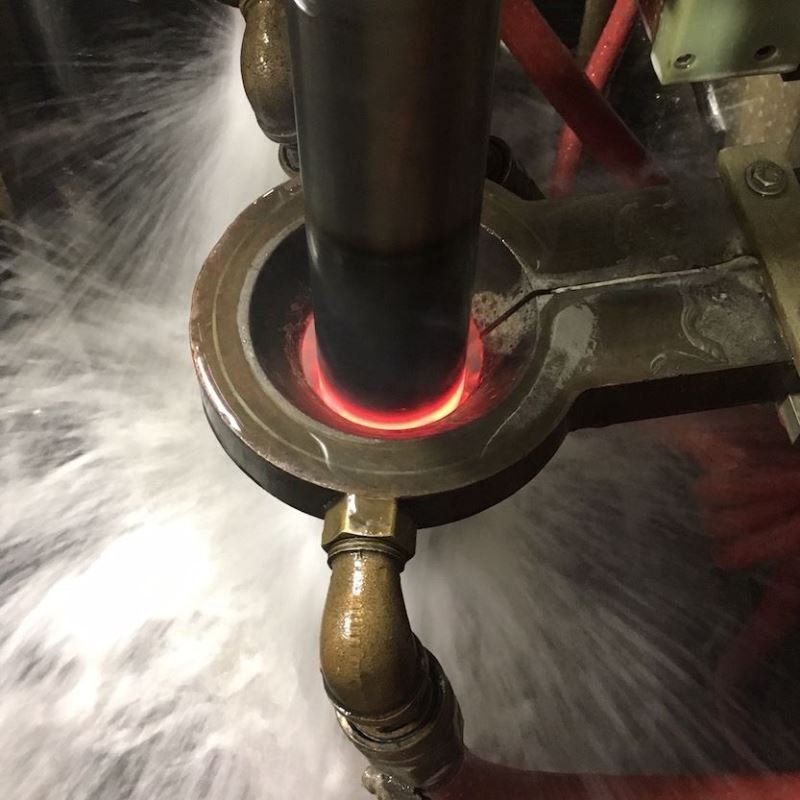
Process and Purpose: By selectively hardening the outer surface, case hardening significantly improves wear resistance without compromising the core’s toughness, ductility, and strength. The process typically involves altering the crystal structure or adding new elements to achieve a thin, hardened surface layer. Case hardening is employed when there’s a need to enhance the surface hardness of softer materials, such as iron or low-carbon steel parts.
When Is Case Hardening Used?
- Low Budget:In situations where budget constraints are critical, case-hardened low-carbon steel offers a cost-effective alternative to expensive tool steels.
- Unique Properties:Parts with a combination of a soft interior and a hard outer layer, like case-hardened couplings, provide durability and strength. These parts can handle misalignments better than through-hardened counterparts.
- Reduced Material Availability:When specific tool steel grades are unavailable in required sizes, opting for case-hardened low-carbon steel becomes a practical solution, especially for non-critical applications.
- Application-Based Use:For applications requiring only a hard surface, case hardening is preferred over through hardening. Examples include files, bolts, and gears.
Case Hardening Methods:
- Heating and Quenching:This traditional method involves exposing the steel part to high temperatures, inducing a change in crystal structure, and then rapidly cooling it to achieve martensite formation.
- Carburizing:When carbon levels are insufficient, carburizing is employed to introduce carbon to the metal’s surface. This process is carried out through pack, liquid, or gas carburizing methods.
- Nitriding:Suitable for steel alloys with elements like aluminum, chromium, and molybdenum, nitriding involves heating the part in the presence of nitrogen gas to form nitrides, increasing surface hardness.
- Cyaniding:In this process, carbon and nitrogen are diffused in the presence of a cyanide-based salt, followed by quenching to achieve case hardening.
- Carbonitriding:Similar to carburizing but in an ammonia environment, carbonitriding adds both carbon and nitrogen to the steel surface, resulting in enhanced hardness.
- Ferritic Nitrocarburising:This method adds carbon and nitrogen to the steel while it’s in the ferritic phase, offering an alternative approach to traditional case-hardening processes.
Carburizing & Annealing
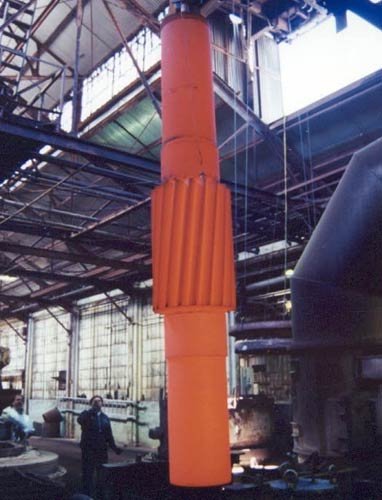
The essence of carburizing lies in infusing carbon into the steel surface, forming a durable case, while maintaining a comparatively softer core. This technique is particularly advantageous for producing robust and highly hardened surface parts with intricate and complex shapes, using cost-effective materials that can be easily machined or formed prior to heat treatment.
Typically, carburizing is carried out by heating components in either a pit furnace or a sealed atmosphere furnace, introducing carburizing gases at the desired temperature. Gas carburizing allows precise control over both the process temperature and the carburizing atmosphere, ensuring optimal results. The process is time and temperature-dependent, with the carburizing atmosphere introduced for the necessary duration to achieve the desired case depth. Careful control of carbon potential prevents excess carbon in the surface layer.
Following carburizing, the workpiece is either slow-cooled for subsequent quench hardening or directly quenched into oil. The choice of quenching method aims to achieve optimal properties with acceptable dimensional changes. Hot oil quenching is employed for minimal distortion, but its application may be restricted by product strength requirements. Press quenching is an alternative for bearing races, maintaining dimensional tolerances and reducing the need for extensive post-heat treatment grinding. In certain cases, tempering is followed by cryogenic processing to convert retained austenite to martensite, subsequently retempering the product.
Metlab possesses the capability to carburize and harden a range of components, from gears to larger items up to 14 feet in diameter and 16 feet tall, weighing up to 50,000 pounds. The facility accommodates shallow cases measuring only 0.002 to 0.005 inches and deeper cases of up to 0.350 inches, meeting specified requirements effectively.
The press quenching apparatus at the facility ensures precise dimensional control, facilitating the accurate hardening of gears and bearings with a diameter of up to 16 inches.
Facilities:
- Gas Carburizing/Carbonitriding (1500° – 1850°F)
- Maximum Load Sizes:
- Pit Furnace: 180″ Diameter by 144″ High
- Pit Furnace: 144″ Diameter by 96″ High
- Pit Furnace: 36″ Diameter by 60″ High
- Pit Furnace (2): 54″ Diameter by 180″ High
- Bell Furnaces (4): 72″ Diameter by 84″ High
- Integral Oil Quench Furnaces: 24″ x 36″ x 24″ High, 18″ x 24″ x 18″ High
- Car Bottom: 78″ Wide by 78″ High by 192″ Long
- Rotary Hearth Furnace and Press Quench: Up to 16″ Diameter Parts
Solutionizing & Aging
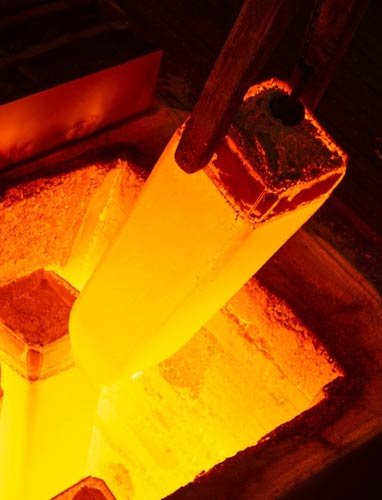
Explore the Expertise of Sun Rise Head Engineers in Solutionizing and Aging Processes:
Solutionization Treatment Process
In the course of manufacturing, materials often undergo hardening, limiting the potential for further processing. Sun Rise Head Engineers’ solutionization treatment, conducted during curing (pressure relief), alleviates the working cure condition, allowing for subsequent curing.Processes like soldering, welding, flame cutting, and laser machining can adversely affect material properties, mitigated through solution annealing before further processing.Premature initiation of final hardening during the manufacturing process, known as precipitation aging, can be averted by re-melting prior to subsequent processing.
Solutionization Treatment Process
In the course of manufacturing, materials often undergo hardening, limiting the potential for further processing. Sun Rise Head Engineers’ solutionization treatment, conducted during curing (pressure relief), alleviates the working cure condition, allowing for subsequent curing.Processes like soldering, welding, flame cutting, and laser machining can adversely affect material properties, mitigated through solution annealing before further processing.Premature initiation of final hardening during the manufacturing process, known as precipitation aging, can be averted by re-melting prior to subsequent processing.
Aging Process
To achieve specific alloy microstructures necessary for meeting part design criteria, materials (cast/worked material) are subjected to prolonged low temperatures. This precipitation aging hardening treatment or structural hardening treatment involves hours of heat treatment, often performed during or at the end of manufacturing. This significantly increases material hardness, leading to predictable volume changes (shrinkage) that must be considered. Subsequent grinding, if needed, can escalate milling costs.Contact Sun Rise Head Engineers today to explore how our Solutionizing and Aging Process in Pune can be the ideal solution for your product. We, at Sun Rise Head Engineers, take pride in delivering optimal methods to enhance the durability of metal-related materials used in various industries.
Enhance the Durability of Metals with Our Solutionizing and Aging SolutionsTo achieve specific alloy microstructures necessary for meeting part design criteria, materials (cast/worked material) are subjected to prolonged low temperatures. This precipitation aging hardening treatment or structural hardening treatment involves hours of heat treatment, often performed during or at the end of manufacturing. This significantly increases material hardness, leading to predictable volume changes (shrinkage) that must be considered. Subsequent grinding, if needed, can escalate milling costs.Contact Sun Rise Head Engineers today to explore how our Solutionizing and Aging Process in Pune can be the ideal solution for your product. We, at Sun Rise Head Engineers, take pride in delivering optimal methods to enhance the durability of metal-related materials used in various industries.
Recognizing the paramount importance of end products offering exceptional quality and purity to customers, we invest significantly in our machinery. Stringent quality control standards are implemented to ensure high standards at all stages of the solutionizing and aging treatment process. Our adept team excels in performing solutionizing and aging across diverse projects. Connect with Sun Rise Head Engineers now to discover how we can contribute to the success of your next project.
Normalizing
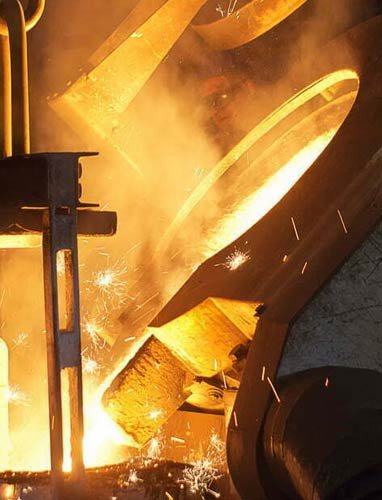
Metals Suitable to be Normalized
For the normalizing treatment of a metal, it must be receptive to normalizing. Various metals and alloys are suitable to be normalized like
- Iron-based alloys like Carbon steel, stainless steel, alloy steel, cast iron, etc.
- Nickel alloys
- Copper
- Aluminum
- Brass
Purpose of Normalizing
The main purposes of the normalizing heat treatment on metals are:
The Normalizing Process
Similar to annealing the normalizing process also follows three main stages; the Recovery stage, the Recrystallization stage, and the grain-growth stage. In the recovery stages of normalizing, the internal stresses are relieved by heating the material. Then the metal is heated to elevated temperatures above the recrystallization temperature of the metal where new grains are formed. Finally, in the grain growth stage of normalization, the grains develop fully when the material is cooled by air.
Applications for Normalizing
Normalizing treatment finds broad practical applications across several industries like Aerospace, Automotive, Heavy Equipment, Energy, Agriculture, Oil & Gas, etc. Usually, whenever metal is expected to get high residual stresses due to some kind of manufacturing steps, it is always suggested to normalize the metal using the normalizing heat-treatment process. A few examples include:- To remove structural irregularities or impurities and defects from the metal.
- To improve ductility that has been lost in some metal processing.
- To reduce the hardness that has been increased by mechanical or thermal hardening processes.
- To increase the toughness of the metal.
- To relieve internal stresses.
- To get an improvement in machinability.
- Carbon steel is normalized when it is cold-rolled to reduce brittleness and increase ductility.
- After work hardening of ferritic stainless steel stampings in the automotive industry, they are normalized to regain their mechanical properties.
- After the thermal microstructure alteration during welding in nickel-based alloys in the nuclear industry, normalizing is performed.
- Steel is heated to about 40-500C (Refer to Fig. 1) above the upper critical temperature (A3 or Acm).
- The alloy is then held at that temperature for around 10-20 minutes.
- Cooling it in still or slightly agitated air to bring back to room temperature.
Annealing
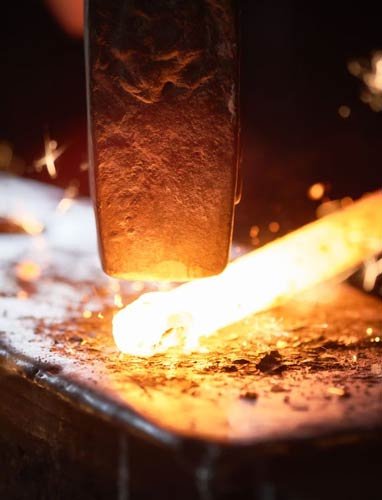
When Is Annealing Used
Annealing creates softer steel than tempering and is thus mostly used on products that do not need to endure substantial stresses. But there are many different instances when annealing is used on metal parts
- Reversal of work hardening
- Softening of weld solidification
- Development of electrical conductivity
- Removal of residual stresses
Reversal of work hardening
Annealing is usually done after a product undergoes mechanical operations that lead to hard and brittle metals. Bending, forming, rolling, grinding, and drawing are all apt examples of such operations. For instance, when a metal wire is drawn to reduce its size, it develops internal stresses and hardens.
The resultant hardness in worked metals makes further processing difficult and risky as the metals may crack. But further processes are an operational requirement. Thus, to return a metal to its pre-work state and make it more acceptable to subsequent operations, we carry out process annealing.
Annealing increases the ductility of the metal and reduces its hardness. This makes the workpiece more formable and machinable. Annealed metals can thus undergo further operations.
The annealing process is especially useful when manufacturing complex parts. As we need to carry out many operations, the annealing process helps us return the part closer to its pre-work state after every operation.
Softening of weld solidification
High-temperature welding processes can cause the formation of heat-affected zones (HAZ). These zones are characterised by having high hardness and brittleness. In such cases, annealing returns the HAZ’s properties closer to its original mechanical properties.
Development of electrical conductivity
Annealing can also affect the electrical properties of a metal. Thus, it is also utilised to improve the electrical conductivity of certain metals.
Removal of residual stresses
Besides affecting the formability and machinability of a material, cold working also causes internal stresses to the material. Even when there are no further operations to be performed, it is a good practice to relieve the internal stresses that crop up after various mechanical operations.
Not addressing them can lead to cracking, material fracture, distortion and other mechanical issues in the future.
Annealing enables us to relieve residual stresses and regain uniform properties in the material. This increases the service life and operational capabilities of the selected materials.
The Annealing Process
The annealing process can be divided into three distinct stages.
- Recovery stage
- Recrystallisation stage
- Grain growth stage
Recovery Stage
In the recovery stage, we heat the metal to a predetermined temperature below the melting point. A heating device such as a furnace or oven is used for heating in a controlled and consistent environment.
The furnace heat reduces the number of dislocations as the atoms start migrating in the crystal lattice. This returns ductility and reduces the hardness of the material. The migration processes also eliminate internal stresses and thus this stage is known as the recovery stage.
Recrystallisation Stage
Once the desired temperature is achieved, we heat the metal further up to its recrystallisation temperature. The recrystallisation temperature also lies below the metal’s melting point. This is the same temperature that is targeted when normalising metal products.
Upon achieving this temperature, we hold the metal at it for a set amount of time. The duration depends on the desired properties and metal grade.
In this stage, the crystal structure begins reorganising itself and the formation of new grain structures begins. This reverses the effects of hardening and helps return the material properties to their pre-work levels.
Grain Growth Stage
The grain growth stage increases the size of the newly formed as well as the former grains once the cooling begins. Factors such as the cooling rate, atmosphere and material grade determine the phase composition and the crystal grain size and growth.
Steel and other ferrous metals are typically cooled to room temperature in the presence of still air. On the other hand, metals such as copper and brass may be either cooled slowly in air or quickly drenched in water. Compared to normalising, the cooling rate in annealing is slower.
Sometimes further operations may be required after annealing to attain the desired mechanical and chemical properties in the material.
The Benefits of Annealing
The annealing process provides the following benefits.
- Increased ductility
- Increased toughness
- Increased machinability and formability
- Reduced hardness to match acceptable levels
- Reduced or completely eliminated internal stresses
- Improved homogeneity
- Improved appearance
- Better chemical and wear resistance
- Improved magnetic properties and electrical conductivity
- Reduced shrinkage
Stress Relieving

Application & materials
Stress relieving does not change the material’s structure and does not significantly affect its hardness.
Hardened and tempered parts to be stress relieved must be treated at a temperature around 50°C below the temperature used for previous tempering to avoid an impact on the hardness.
Stress relieving before nitrocarburising should be executed at temperatures >600°C.
Copper and brass components can also be stress relieved. For stainless steels a high temperature solution heat treatment is normally necessary.
Process details
The stress relieving temperature is normally between 550 and 650°C for steel parts. Soaking time is about one to two hours. After the soaking time the components should be cooled down slowly in the furnace or in air. A slow cooling speed is important to avoid tensions caused by temperature differences in the material, this is especially important when stress relieving larger components.
If necessary, stress relieving can be performed in a furnace with protective gas, to protect surfaces from oxidation. In extreme conditions vacuum furnaces can be used.
The temperature for stress relieving copper parts is, depending on the alloy, 150-275°C and for brass components 250-500°C.
Stabilizing
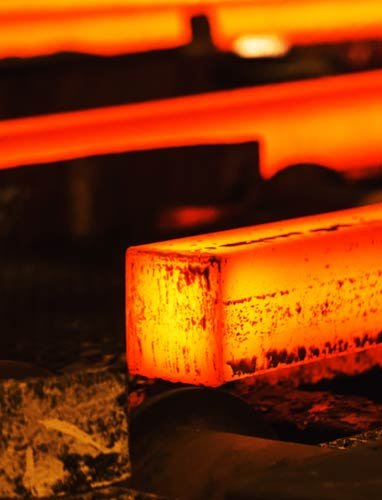
- Ensure that the material is clean and free from contaminants before the heat treatment process begins.
- Verify that the material is in the proper condition for stabilization, as different alloys and materials may have specific requirements.
Annealing
- Stabilizing heat treatment often involves annealing, which is a controlled heating and cooling process. Annealing helps relieve internal stresses and promotes grain refinement.
- The material is heated to a specific temperature and held at that temperature for a set period, allowing the internal structure to reach a more stable state.
Temperature Control
- Precise temperature control is crucial for a successful stabilizing heat treatment. Use calibrated equipment to monitor and control the temperature within the desired range.
- Follow recommended temperature profiles based on the material type and desired properties.
Hold Time
- The material needs to be held at the annealing temperature for a sufficient duration to allow for proper diffusion and stress relief. The hold time depends on the material and its thickness.
Cooling Rate
- Control the cooling rate after the material has been held at the annealing temperature. Slow and controlled cooling helps prevent the formation of new stresses and ensures a uniform structure.
- Consider using a furnace with programmable cooling rates for more precise control.
Protective Atmosphere
- Depending on the material, it may be necessary to carry out the heat treatment in a controlled atmosphere (e.g., inert gas) to prevent oxidation and decarburization.
Monitoring and Quality Control
- Regularly monitor and record temperature profiles during the heat treatment process.
- Perform quality control checks on the finished product to ensure that the desired properties have been achieved.
Post-Heat Treatment Processing
- Depending on the application and material, additional processes such as quenching or tempering may be required after stabilization to achieve specific mechanical properties.
Documentation
- Maintain detailed records of the heat treatment process parameters, including temperature profiles, hold times, and any deviations from the standard procedure.